State of the art tool making facilities in house, to your specification
The first stage in the design and development process. J Coker’s on-site tool room is headed up by Andrew Coker, a highly experienced tool maker.
Working with his team of CAD Designers and CNC operators we can take any concept through to successful production.
Hours
8-5pm
Mon - Fri
(open until 1pm on Friday)
Service area
Worldwide
Contact our tool making specialist
01795 535008
info@j-coker.co.uk
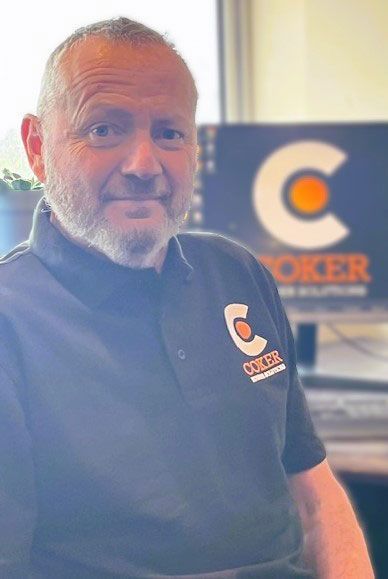
- Prototyping – we can help develop your concept or design into reality by making single impression prototype tools. This gives you an advantage over 3D printed test pieces as tooling can also experiment with hardness and material type, and completely reflective of the final product.
- Prototyping keeps your costs to a minimum and can help finalise design in a low cost timely manner.
- Reverse engineering – we can take deteriorated and worn parts and reimagine them as new.
- Flexible file formats and access – drawings can be accepted in CAD file format or hard copy (sketch or PDF). The most common formats are DXF, STEP and IGES.
- All tooling is sampled for your approval. ISIR documentation is available on request.
- Ownership – tools remain the property of our clients. We are happy to store them for you, fully insured, at our premises for fast turnaround of moulding production runs.
- You are welcome to take tooling in-house for your own production purposes – we are highly experienced in making tooling for Rubber Moulding, Polyurethane and Plastics.
- Capabilities: HAAS Tool Room Mills, HAAS CNC Lathes, Spark Eroding Facilities, Electrode Manufacture, Turning, Milling and Surface Grinding, Welding and Cylindrical Grinding.
- Single cavity to multi-cavity tooling – suitable for compression, transfer or injection moulding processes. We have a Boy 22 vertical injection moulding machine for small prototypes.
- Acid etching for superfine finishes.
- Shadow Graph measuring facilities for accurate fine details.
Toolmaking: CASE STUDY
"Cokers have been an excellent partner in our tooling needs. They understand the challenges faced and go above and beyond to meet our specific requirements and tight deadlines. The expertise and knowledge Andy has is second to none in the toolmaking industry and we really value our relationship with Cokers”.
Dean Wealleans | Managing Director
Ley Holdings, including Ley Rubber and COH Baines.
COH Baines are a market leader in the production and supply of rubber and plastic extrusions and mouldings. An independent UK Company with more than 80 years’ experience; they stock a wide range of extrusion profiles and moulded products to supply a diverse range of industries; from Aerospace, Automotive, Construction, Electronics, and Engineering to Leisure Industries including, Caravans, Classic Cars and Marine with a variety of moulded items.
They are also the sister company of Ley Rubber Ltd, a long established and well-regarded supplier of extrusions and mouldings.
COH Baines approached Cokers in late 2018 with a tool making proposal. They had identified a number of products that would expand COH’s product offering to their customers, particularly those in the classic car market.
A number of rare OEM parts had been sourced which were no longer readily available in the marketplace. They were looking to find a UK tool maker, with the capabilities and experience to reverse engineer these parts and supply COH Baines with their own custom-made tooling which they could then mould in-house. The array of tools needed meant they needed a committed supplier that would work to their priorities and deadlines.
Tooling Design
Many of the parts supplied were deteriorated from weather conditions, notably a variety of rubber quarter-light window seals.
Interpreting and replicating the parts was the key challenge faced by our CAD design specialist. For example, a quarter-light would have multiple profiles within it, each necessary to form the exact fit to the door and window frame.
Each separate section had to be scanned and modelled and like a jigsaw puzzel, put back together again. With Andrew’s knowledge of the practicalities of rubber moulding and de-moulding, Andrew was able to use this expertise in the design process, to enable to complex parts to be made using compression moulding techniques.
From the simple to the complex, Cokers are proud to supply tool making services to COH Baines, and their sister company Ley Rubber with custom made tools.
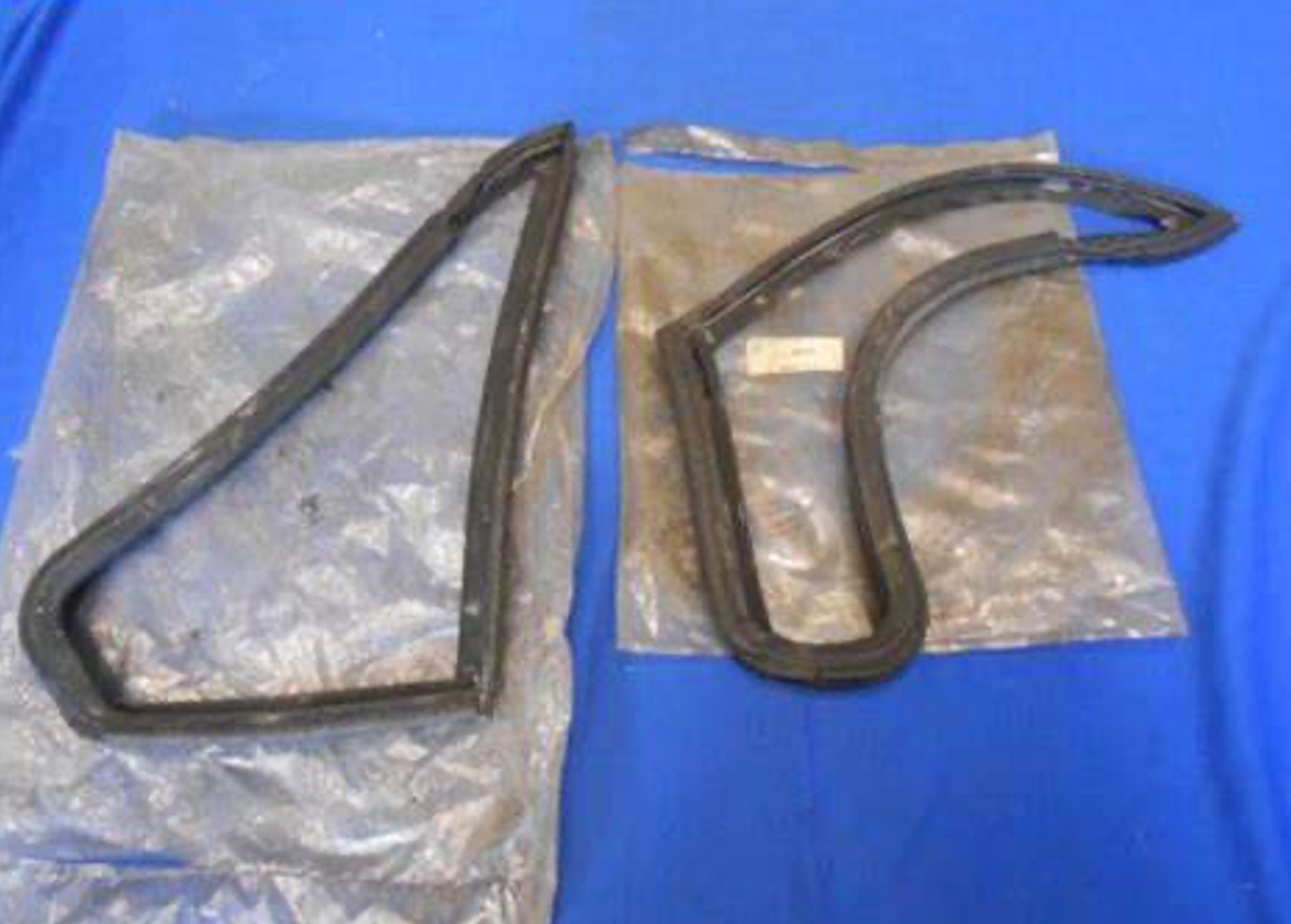
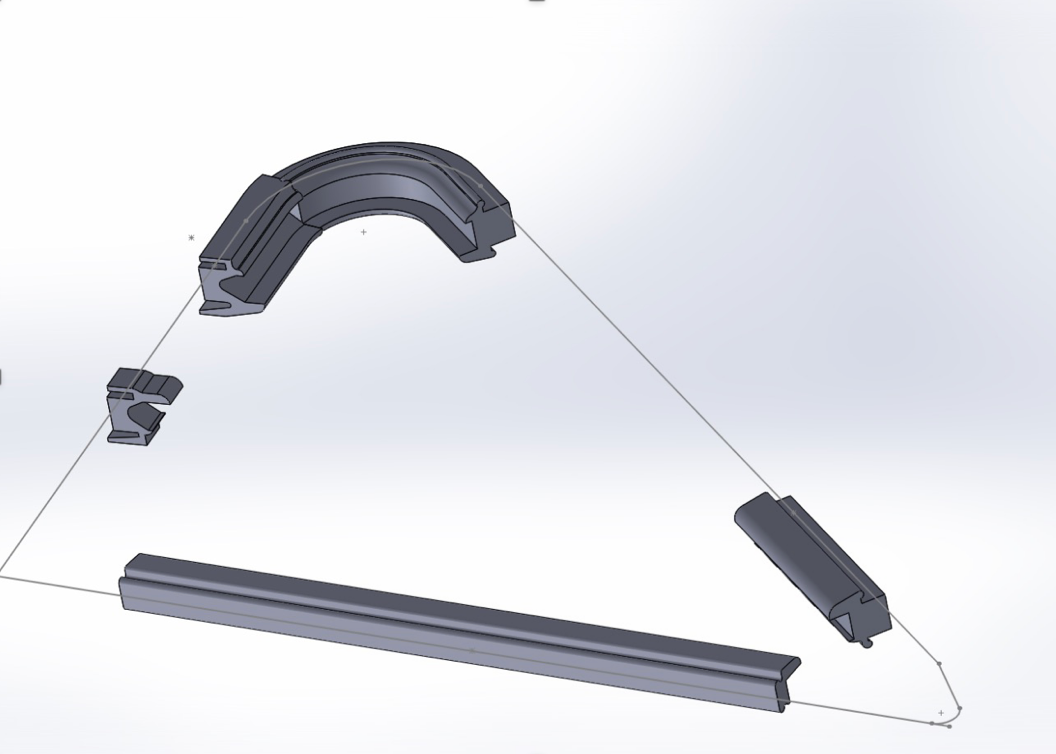
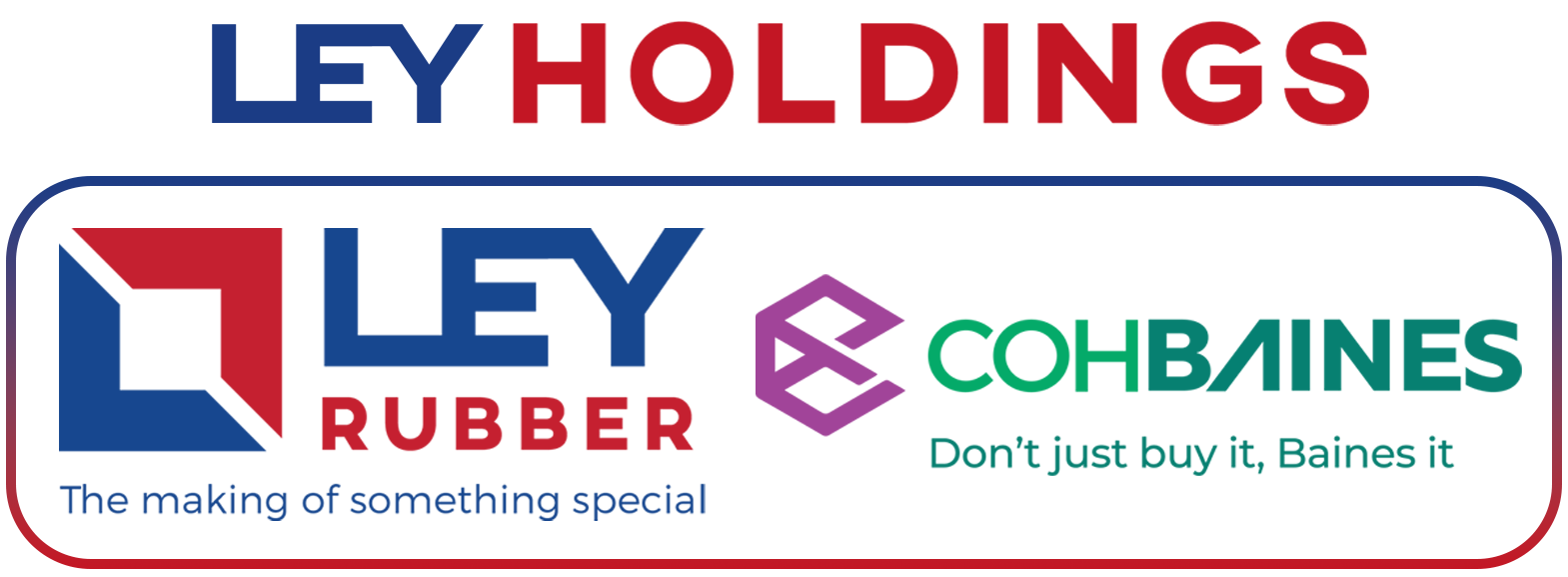
Our methods
Tool moulding
The first stage in the design and development process. J Coker’s on-site tool room is headed up by Andrew Coker, a highly experienced tool maker.
Fabrication
Fabrication services covers a multitude of products, particularly those too large to be moulded. From hand-made bellows and sleeves and rubber lined pipes to cut gaskets, washers and rubber sheeting.
Casting discs
We manufacture our own range of rubber and silicone casting discs for centrifugal casting.
We are happy to recommend J Coker Ltd for all our tool making services.
Russell Mewett, Director, Mewett Polyurethane
Coker’s always do more than is necessary, they are a pleasure to work with.
Brent Hallo, CEO Fitness Professionals.
Coker’s are an absolute pleasure to work alongside, we would be simply lost without them.